Tracking construction equipment across multiple job sites and managing maintenance and allocation for projects are complex and time-consuming tasks. Manual monitoring by employees often leads to inefficiencies and human errors, impacting productivity and project timelines.
An AI-powered asset tracking system streamlines equipment management by automating these tasks, reducing errors, and freeing up employees to focus on their main responsibilities. Once considered a tool for large corporations, AI is now going mainstream, enabling small and medium-sized businesses (SMBs) to implement it and gain a competitive edge.
What Is Involved In Equipment Tracking And Management
Effective equipment tracking and management ensures that machinery and tools are readily available, well-maintained, and utilized to their full potential.This process involves a range of tasks, that traditionally required a lot of manual processing and employee time. Modern asset tracking methods, such as QR code asset tracking, BLE asset tracking, and IoT asset tracking , automate these tasks, reducing reliance on manual labor. The AI-powered asset tracking system works in sync with these methods, helping companies automate tasks, efficiently process and analyze data, and make informed decisions.
Equipment Inventory Management
Companies need to have accurate and up-to-date records of all equipment, including serial numbers, specifications, maintenance records, and job assignments. This is typically accomplished by manually updating logs or spreadsheets (inefficient), or keeping track of this data in the centralized asset management system (more efficient). Periodic physical inspections of the job sites may be required to ensure accurate equipment records.Equipment Location Tracking
Companies need to know current location of the equipment, as well as its movement history and past usage for the projects. Such tracking ensures that equipment is available when and where it is needed, prevents equipment misplacement, loss and theft.Although some companies are still trying to keep track of equipment location with spreadsheets, most use more advanced methods - such as mobile systems with QR code scanning and a centralized cloud data storage.
Equipment Allocation for Jobs
Companies need to assign equipment to the jobs based on project requirements and availability. Allocation equipment for the jobs ensures that the right tools and machinery are available for each project, there are no shortages and delays.Asset management software systems usually have the tools for assigning equipment to the jobs. AI can take this task to the next level, analyzing data and suggesting the most optimal equipment allocation.
Equipment Preventive Maintenance
To prevent equipment breakdowns and costly downtime, companies must monitor equipment usage and conduct preventive maintenance at pre-scheduled intervals. Employees can keep a manual log of maintenance dates and fill out paper maintenance form, which is very inefficient. More advanced methods include a centralized equipment maintenance system and mobile forms.Equipment Utilization Optimization
In order to extend the lifespan of equipment and maximize its efficient use — reducing the need for rentals — companies must analyze how frequently and effectively their equipment is utilized. While asset management systems offer usage data that help with deployment planning, AI takes this task a step further. It can analyze data from multiple sources more effectively than a human, creating highly efficient utilization plans tailored to the company's needsCompliance and Documentation
Construction industry is highly regulated, and a lot of paperwork is required to ensure compliance. The paperwork may include safety inspections, audits, maintenance records, and more.Traditionally companies were relying on the paper forms, which are now being replaced by digital mobile forms, that can be filled out on a smartphone and submitted to a centralized cloud system for on demand access.
Challenges of Traditional Asset Management Methods
Without automation, equipment tracking and management tasks demand constant attention and effort from company employees, often leading to:- Human Errors Manual data entry and tracking increase the likelihood of mistakes.
- Inefficiency Valuable time is spent on repetitive manual tasks.
- Lack of Visibility Real-time updates are rare, leading to delays and miscommunication.
Modern AI-powered asset management systems can eliminate these problems by automating key tasks, improving accuracy, and providing actionable insights.
AI Applications For Equipment Tracking And Management
An AI-powered asset tracking system can help you automate equipment management tasks, increasing efficiency and reducing human errors. Here are key areas where AI can streamline your processes, delivering better results with less effort.How AI Enables Real Time Equipment Tracking
In construction and field service industries, where equipment is often spread across multiple job sites, knowing the exact location of machinery and tools at any given moment is crucial. Misplaced equipment can lead to project delays and increased costs.AI-powered asset management systems, combined with advanced tracking technologies, offer a real time equipment tracking solution that is automated and accurate. The system that combines IoT and AI creates unique benefits for businesses. IoT sensors, electronic tags for assets and inventory (such as BLE and RFID), or GPS tags can continuously capture data on equipment location, movement, and usage. AI algorithms process and analyze this data, producing human readable reports that authorized employees can access on demand from anywhere.
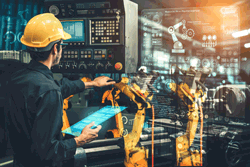
Equipment Predictive Maintenance Using AI
Predictive maintenance is a key application of AI in equipment management. Instead of relying on fixed maintenance schedules or reacting to equipment failures, AI system allows companies to monitor equipment conditions in real time and predict potential issues before they occur. This approach minimizes downtime, reduces repair costs, and extends the lifespan of equipment.AI-powered predictive maintenance systems analyze data from IoT sensors, such as vibration levels, temperature, pressure, and operational hours, to identify patterns and anomalies that signal potential problems. By processing data received from the sensors, AI can detect early warning signs before a human operator could, and send an alert to the maintenance team. Timely alerts allow maintenance crew to address the problem proactively, and schedule repairs during non-peak hours, avoiding costly disruptions to projects.
This approach not only prevents equipment breakdowns and downtime, but also optimizes resource allocation. It helps companies to focus maintenance efforts where they are most needed, reducing unnecessary services of the well-functioning equipment.
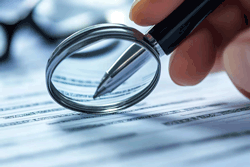
Automating Equipment Inspections With AI
AI integrated with IoT sensors automates equipment inspections and the associated paperwork, reducing manual effort and improving accuracy. Instead of sending an employee to periodically perform an inspection and filling out a form, AI powered equipment management system continuously processes key parameters sent by the sensors and cameras, identifying issues as they happen.The system eliminates the need for manual documentation. AI system automates data entry, generates detailed inspection reports, and ensures compliance with regulatory requirements.
For example, after analyzing inspection results, AI-powered equipment management system can produce an inspection report, outlining equipment conditions and providing recommendations. AI system not only maintains proper documentation on its own, but also enables proactive issue resolution, helping companies minimize downtime and maintain safety standards.
Using AI For Equipment Access Authorization
AI-powered equipment management system can help companies verify that only authorized personnel have access to the equipment. Such verification is important for operational safety and security. By integrating advanced technologies, such as biometrics, machine learning, and IoT-enabled devices, AI can automate and strengthen access management processes.One of the key methods AI employs is biometric verification, such as facial recognition, fingerprint scanning, or iris detection, to authenticate users. Only individuals whose credentials match the stored data are granted access. AI systems can also assign permissions based on the employee role and certifications.
In addition to employee verification, AI system can analyze user behavior to detect anomalies. For instance, if a user attempts to access equipment at unusual times or from an unexpected location, the system can flag the activity for further review or deny access altogether.
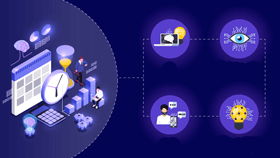
Optimizing Equipment Job Allocation With AI
One of the things that AI can do better than humans is to analyze large amounts of data from multiple sources, and reach conclusions based on the data analyzis. This ability works well when it comes to equipment allocation and utilization planning.Traditional methods often rely on manual assessments or static schedules, which can lead to underutilized assets or delays caused by equipment shortages. AI eliminates these inefficiencies by processing data such as job requirements, equipment availability, and usage history to recommend the optimal allocation of machinery across projects.
For example, AI-powered equipment management system can monitor which equipment is idle and identify opportunities to redeploy it to other job sites where it’s needed. It can also predict future demand based on project timelines, weather conditions, and historical data, enabling proactive planning.
By optimizing equipment allocation, AI reduces idle time, minimizes rental costs, and ensures that each piece of equipment is used to its full potential.
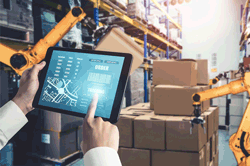
Optimizing Spare Parts Stock Levels and Automating Reordering with AI
Use AI to maintain the optimal level of spare parts for equipment service, maintenance and repairs. AI-powered system can analyze data on equipment usage, maintenance, and historical consumption patterns to determine the quantity of spare parts needed at any given time. It also takes into account seasonal trends, equipment wear rates, and upcoming projects. Such analysis helps you maintain optimal stock level of spare parts, avoiding over-stocking that ties up capital and storage space, and stockouts that cause project delays.When stock levels approach a critical threshold, the system can automatically generate purchase orders, ensuring timely replenishment without manual intervention.
AI Equipment Management Implementation Steps
Implementing AI for equipment management can seem complex, but breaking it down into clear, manageable steps ensures a smooth transition and maximizes the benefits. Here are the key steps involved in implementing AI for streamlining equipment management process:Assess Your Needs and Goals
Start by identifying specific challenges in your current equipment management processes. Perhaps, your weak spot is equipment location tracking. Or you are having a hard time keeping up with equipment maintenance. Maybe you are struggling with equipment allocation, or constantly running out of spare parts.Do not try to cover everything at once. Define the most pressing needs that you have, and concentrate on them first.
Choose the Right Technology
Select AI-powered solutions tailored to your specific goals and requirements. If you need to track equipment location, select which tracking devices will work best for your use case: GPS, BLE or RFID. If you need predictive maintenance, or would like to automate equipment inspections, select the right types of sensors and IoT gateways. If, on the other hand, you are most interested in AI analyzing and reporting capabilities, select an AI system with strong machine learning algorithms.Integrate AI with Existing Software Systems
Ensure the AI system works well with your current asset management, ERP, or other internal software systems. This integration helps centralize data and provides a unified view of your equipment operations.Start With A Pilot Project
Once you identified the most pressing needs, and technology you need for it, Select a specific area or job site to implement a pilot project. This controlled environment will allow you to evaluate the AI system's performance, gather employees feedback, and address any challenges without disrupting broader operations. Focus on areas where AI can deliver quick wins, such as real-time equipment tracking or predictive maintenance.Train Employees
Provide training for your team to understand how to use AI tools effectively. This includes interpreting AI reports, troubleshooting minor issues, and adapting workflows to integrate AI recommendations.Monitor and Refine
After implementation, continuously monitor the AI system's performance and gather feedback. Use this information to refine processes, fine-tune algorithms, and ensure the system evolves based on your business needs.By following these steps, businesses can successfully harness AI's potential to streamline equipment management, improve efficiency, and gain a competitive edge.