Cloud-based centralized inventory management platforms with connected mobile apps are the key to smarter, faster, and more accurate inventory control. Whether you are in the warehouse, on the road, or in the field, a mobile app automates asset and inventory tracking with smart tag scanning (QR codes, NFC, BLE), fast data capture and real time updates. A centralized cloud system connects all team members and devices together, providing real-time visibility into inventory stock and assets location to all team members.
The Power Of Centralized Cloud System For Inventory Management
A cloud inventory system improves inventory management process by allowing real time updates from anywhere, and giving live data access to all authorized software users.What Is A Centralized Cloud Inventory System
A centralized cloud inventory system is a software solution hosted on a remote server. It gathers data from multiple sources: mobile apps, IoT gateways, web interfaces - and consolides it into one unified, real-time inventory hub. All employees, whether in the field, warehouse, or office, can update inventory in real time, with the changes instantly visible to the entire team. Unlike traditional inventory management methods, such as spreadsheets or desktop software, cloud-based platforms with mobile access provide a single source of truth, streamlining operations, improving data accuracy, and helping teams get more done with less effort.A cloud inventory management system typically consists of:
Smart, cloud-based inventory system typically offers features such as:
By moving inventory management processes to the cloud system with mobile access, businesses can reduce costs, improve efficiency, prevent stockouts and overstocks, and deliver a better customer experience.
Why Do Businesses Need Cloud Inventory Management System
Without a centralized cloud-based inventory system managing inventory stock across multiple locations becomes a logistical nightmare. Manual tracking with spreadsheets or desktop software leads to errors, delays, and missed opportunities. Field employees are often left in the dark, unable to access critical inventory data.This lack of visibility can result in costly consequences: overstocking ties up capital, understocking leads to project delays and missed deadlines, and untimely damages your reputation with the clients.
Centralized inventory management systems offer a powerful solution to these challenges.
Components Of A Centralized Cloud-Based Inventory Platform
A centralized inventory management system brings together three essential components: cloud software, mobile applications, and optional IoT devices. Each component plays a distinct role in ensuring real-time inventory visibility, streamlined workflows, and operational efficiency.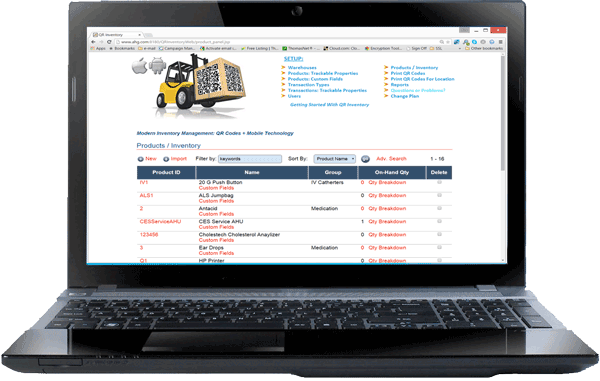
Cloud Software: The Central Brain of Inventory Operations
Cloud software serves as the central command center for your entire inventory system, that handles logic, workflows, and user interaction. Te responsibilities of the cloud software include:- Storing and processing inventory data from all connected sources
- Managing system logic for transactions, validations, and business rules
- Generating reports and analytics that support informed, data-driven decisions
- Synchronizing data in real time across all users, devices and locations
- Enforcing user roles and permissions, ensuring data integrity and access control
This centralized cloud platform ensures that every inventory action - whether from the field, warehouse, or office - is reflected system-wide in real time.
Central Database: The Single Source of Inventory Truth
The central database is the backbone of data integrity in a cloud-based inventory system, solely responsible for storing, organizing, and safeguarding all inventory-related data. Key responsibilities of the central database are:- Persistent storage of inventory transactions, asset records, locations, user logs, data collected via digital mobile forms, asset specs and documentation.
- Ensuring data consistency and accuracy across all connected devices
- Providing fast, reliable access to large volumes of structured inventory data
- Serving as the foundation for reports and data analytics
- Maintaining historical records and audit trails to support compliance and accountability
Whether accessed by mobile apps, IoT devices, or cloud-based dashboards, the central database ensures everyone in the organization is working from the same, always current data set.
Mobile App: The Frontline Interface For Field And Warehouse Teams
Mobile apps serve as the user interface for out-of-office employees. The key responsibilities of the mobile app include:- Capturing inventory movement through scanning, collect data via mobile forms, capturing images, signatures and GPS location
- Providing real-time access to stock levels, asset locations, documentation and specs, and other task-specific data
- Enabling offline work, allowing users to operate in remote areas and sync to the cloud later
- Completing field paperwork (inspections, audits, maintenance logs) using digital mobile forms
IoT Gateways & Sensors (Optional): The Automated Data Collectors
Gateways in IoT asset tracking system act as autonomous observers, continuously monitoring inventory and asset movement without user input. The responsibilities of IoT system include:- Detecting asset and inventory movements in designated monitored areas (warehouses, yards, job sites or even service trucks and trailers)
- Automatically transmitting asset and inventory data to the cloud platform via IoT gateways
- Triggering alerts for misplaced or missing assets
- Providing real-time, accurate asset and inventory tracking in environments where manual scanning is impractical
IoT devices are especially valuable for high-value tools and equipment, or around-the-clock operations where human tracking isn’t feasible.
Use Cases for Smart, Cloud-Mobile Inventory Systems
Together, these components of a centralized inventory management system form a powerful, flexible platform that adapts to various industries and workflows. These are just several examples of how smart inventory management helps businesses in various industries.-
Inventory management For Construction & Field Services
Cloud-mobile inventory system helps construction companies track materials, tools, and equipment as they move between job sites, storage yards, and vehicles. Mobile apps allow field crews to log deliveries, usage, and tool check-ins in real time. BLE or RFID tags automate tracking of high-value assets, such as generators and power tools.
More on construction inventory management More on construction asset tracking More on tool tracking -
Inventory Management For HVAC, Plumbing, Electrical & Other Mechanical Contractors
With the centralized cloud system mechanical contractors can be sure that service trucks are stocked with the right tools and parts before dispatch. Mobile apps help technicians update inventory on the go, record equipment usage, and submit digital forms for maintenance or service records. Tools check out / check in system in the mobile app, with images and signature capture increases tool accountability and reduces equipment loss.
Inventory software for HVAC & plumbing contactors Inventory software for electrical contractors Inventory & tool tracking for roofing contractors -
Asset Management System For Oil & Gas
Cloud inventory system, with mobile access and BLE asset tracking option allows oil & gas companies to monitor parts, equipment, and consumables across remote drilling sites and production facilities. Mobile app works in the connected and offline mode, so field employees can track assets and inventory, as well as record data in remote areas with no connectivity. BLE tags, IoT gateways and sensors provide automatic updates on equipment movement, conditions, and status.
More on oil & gas asset management -
Smart Warehouse Inventory management
Warehouse industry benefits from barcode and QR code scanning on mobile devices for fast inventory tracking. Warehouse employees can quickly scan-in batches of received inventory, record storage location within the warehouse, quickly find items for picking and packing using a mobile app, and record inventory shipping. BLE tags and IoT gateways help automate warehouse pallet tracking. A centralized cloud inventory system makes it easy to coordinate fulfillment, replenishment, and cross-docking across multiple locations. For perishable good an IoT temperature and humidity monitoring system provides automated remote control 24/7, preventing waste and spoilage of warehouse goods.
Smart warehouse inventory software with climate control BLE warehouse inventory management -
Traceability For Healthcare & Lab Environments
Cloud-mobile inventory system helps labs and healthcare facilities track inventory by lot numbers and maintain traceability, without spreadsheets and tons of physical paperwork. Mobile app allows employees to scan lot numbers of serialized inventory and record all necessary info as materials go through the process. The traceability info is safely preserved in the cloud for regulatory compliance, quality audits, and instant retrieval whenever it is needed.
Lab inventory management & traceability